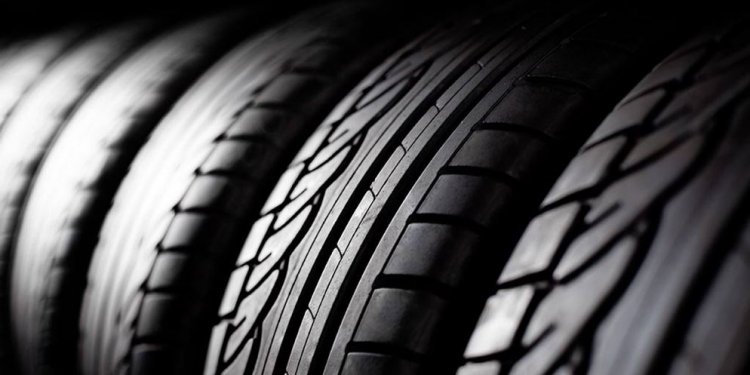
Automotive industry Group
As somewhere else, the usage of green garbage as support fibres has been playing a previously increasing role in the automotive business in the past several years. Modern-day vehicles now contain on average five to seven kilogrammes of normal fibre products. In German luxury cars, more or less 90per cent of interior furnitures are constructed of natural fibre-reinforced plastics (NFP), plus mid-range automobiles that figure is mostly about 60per cent: programs include interior home trim, boot linings, free wheel wells and covers, line trim, tool panels, roof linings, air flow displays, parcel shelves, glove cardboard boxes, and seat shells and backs. But NFP normally witnessing increased usage in outside components. The standard manufacturing underbody regarding the Mercedes A and B-Class, including, is reinforced with abaca fibres by means of effect extrusion. Besides circulation- and compression-moulded components in particular, NFP-based elements created by injection moulding offer plenty of prospective worth exploiting.
At Ford, researchers have already been researching to incorporate all-natural materials into automotive building since the business had been established over one hundred years ago. These days, above 300 components made from all-natural products are generally found in Ford cars – including, amongst others, the Fiesta, the Focus and the Mondeo. The all-natural products tend to be incorporated mostly in which they can't be seen: in instrument panels, door trim or bumper methods, as an example. ‘We are working intensively regarding the development of bio-based materials. Fibre substances are part of this lasting development method, ’ describes Maira Magnani, Research Engineer for Advanced Materials & procedures at Ford analysis & Advanced Engineering European countries. ‘Applications are increasingly being studied in most areas – such as the motor area, the car inside, and exterior components. The key criterion for assessing in which as soon as it's wise to replace NFP for standard materials is a confident environmental balance sheet. The substitution should never result in increased fat, as an example.’
The advantages of NFP are obvious: unlike standard synthetic support materials such as for example glass fibres, natural fibre products have actually up to 50per cent lower thickness, simultaneously reduce the CO2 impact, and invite not merely much more material recycling additionally 100per cent thermal disposal of this strengthened plastic. In so doing, they open totally new opportunities for this type of lightweight construction product, specially additionally in the field of electromobility.