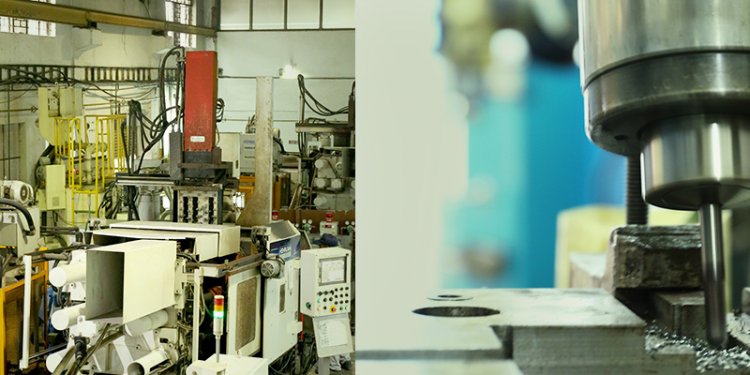
Automobiles Industries
Continuing from my previous post, another example of the part that digital production and simulation plays arises from the Automobili Lamborghini Advanced Composite Structures Laboratory (ACSL) in the University of Washington in Seattle (American), which blends aerospace and automotive composite development. Using Boeing and US Federal Aviation management (FAA), the ACSL improves official certification of the latest composite materials and frameworks, usually based on proven virtual evaluating principles pioneered for Lamborghini automobiles.
ACSL and Boeing worked on advanced analysis means of predicting the crash performance associated with all-composite monocoque of Lamborghini’s Aventador automobile. Aventador passed its crash-test official certification regarding very first try; previous designs needed 2 or 3 examinations. At $1 million per crash, cost savings had been considerable, also without factoring over time and value conserved by not creating additional test cars. See figure above.
A Whole Paradigm Shift
While these types of programs go beyond industry requirements in using virtual evaluation, Dr. R. Byron Pipes, John Bray Distinguished Professor within the university of Engineering at Purdue University (USA), feels they don’t get far adequate.
Current styles in virtual evaluation of brand new composites is only an incremental improvement, Pipes believes, not the whole paradigm move necessary to unshackle composite development. “We are suffering empirical-based manufacturing and (bodily) testing-based official certification, ” he said. “It costs $100 million per product to qualify composites to travel on a airframe. When certified, products changes are economically impossible.”
Dr. Pipes describes composite development these days as dominated by experiments and just assisted by analysis. “We have the computational power to transform this paradigm and replace thousands of (physical) tests with robust multi-scale simulation of manufacturing and performance, ” he stated. “Only then will we enable innovations in materials composition and handling without duplicated pricey recertification.”
Decreasing Uncertainty
Today, producers physically test every element before it is put together and each part before it continues on a plane, causing unsustainable development rounds and prices. “You will never totally escape the necessity for (bodily) testing to verify designs, but we ought to address the matter of certainty in simulation results, or rather, how to manage anxiety, ” Dr. Pipes stated. “Simulation resources can guide knowledge of anxiety in design also exactly how it propagates.”
Making use of digital simulations, Cobham life-support reduced destructive tests on a NASA gasoline tank by 50percent, saving $500, 000.
To demonstrate the possibility for the approach, Dr. Pipes cites the US National Nuclear safety Administration (NNSA).
Because of the US moratorium on nuclear product screening, NNSA, an unit associated with US division of Energy, cannot carry out full-scale real performance examination. “About fifteen to twenty years back, we defined a roadway map of what was needed seriously to attain simulation-based official certification, ” stated Dr. Mark Anderson, technical advisor into the NNSA from Los Alamos National Laboratory, a US federal government- supported research agency. Key elements of this road chart consist of: change to a validated predictive capacity centered on multi-scale, physics-based computer system simulation and measurement of doubt in NNSA’ simulation tools.
Balancing Physical and Virtual
Dr. Anderson feels composites modeling are advanced level by adapting the NNSA strategy. “For most industries, what is the most appropriate is a balance between your historic testing-based method which simulation/uncertainty measurement based strategy, ” Anderson said. He notes that although considerable concept moved into composite industry designs, many however make use of a straightforward mathematical description that fits empirical test information.