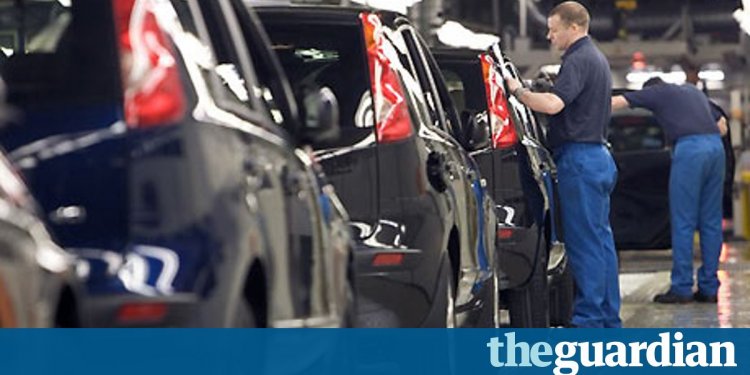
Cost to manufacture a car
© GM
Bob Lutz Weighs In
A Reuters article saying that GM was dropping $49, 000 on each Volt it develops, and therefore every one are priced at $89, 000 to create, produced a bit of an eating madness inside media recently. It's becoming virtually fashionable now to declare that no green technology can be commercially effective (everybody remembers Solyndra, which appears to have unsuccessful more as a result of bad administration than anything else, and no one remembers the Prius...). Today, the father of Volt, Bob Lutz, published a bit in Forbes to guard their baby from people who attack it. The crux of the argument is:The statement that GM “loses” over $40K per Volt is preposterous. What the “analyst” in whom poor Ben Klayman placed their faith did should divide the full total development cost and plant financial investment because of the few Volts produced to date. That’s like saying that an actual property company that sets up a $10 million building and it has local rental earnings of just one million the very first 12 months is “losing” 9 million bucks, or several hundred thousand per renter.
Primer from the price of Making material
This relates to every little thing, therefore let's dig deeper making it clear how things work.Secured Expenses
Therefore let's imagine you will be a manufacturer who would like to make a high-tech product that isn't just a small variation on something which already is out there. You'll first need produce the product, which often suggests investing a couple of years in research & development, purchasing the wages of countless engineers, the expense to build and testing prototypes, market research, finding companies, probably doing a bit of marketing and advertising to create men and women alert to what's coming, etc. Just that stage can cost hundreds of thousands, hundreds of millions, if not billions depending on the product, along withn't made one dollar yet.Then in the event that you decide that you have produce a viable product that people will need it, you'll want to really have the ability to make it. And that means you invest even more millions into building or retooling one or many production facilities where in actuality the product are made. If it is an entirely brand new product, it probably does mean retraining most of your staff members.
All of that is just the fixed prices for the item. Whether afterward you go on in order to make one product or a million, that amount nearly will always be similar (unless you later need certainly to build more production facilities, get even more equipment and hire more folks to improve production capacity). Complete fixed costs can only go up with time, perhaps not down.
The target is usually to amortize, or spread, those fixed costs over as numerous salable item units as you possibly can. It doesn't only mean units sold, however. For instance, the next generation of the Toyota Prius utilized some technologies created when it comes to first-generation. Toyota did not must completely reinvent the wheel, so that the fixed costs sunk into the very first Prius were spread-over multiple generation associated with the automobile. These people were also spread - eventually - unto other designs just like the various other Toyota and Lexus hybrids. This is exactly why establishing the initial hybrid or electric vehicle or whatever is always more costly than subsequent designs.
Variable Expenses
We are not out associated with the woods however. After every one of the fixed costs have already been compensated, you have got adjustable costs. That's what it costs to build every individual unit. Therefore let's imagine that to create a Volt you'll want to get a battery from manufacturers, you may need X level of metal, Y level of copper, Z quantity of plastic, etc... All those and the work costs plus the energy costs to operate the plant are your variable cost per product. In the event that you make even more units, those prices increase proportionally, and in case you make less, they go down.In the long run you and your manufacturers will often enhance numerous processes and take advantage of economies of scale, this may lower variable prices substantially. For example, if in 5 years battery pack pack costs 1000s of dollars less, that may make a big difference when spread-over thousands of automobiles.