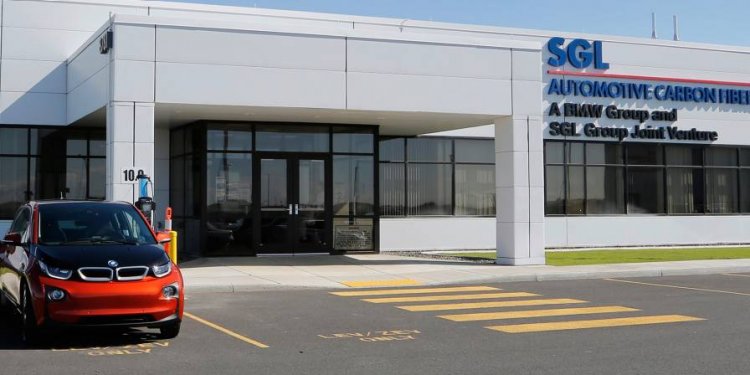
Production Process of automobile industry
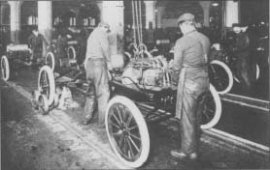
Background
In 1908 Henry Ford began production of the Model T vehicle. Predicated on their original Model A design initially stated in 1903, the Model T took five years to develop. Its creation inaugurated that which we know today given that size production assembly line. This revolutionary concept was on the basis of the notion of just assembling compatible component components. Before this time around, mentors and buggies was in fact hand-built in small figures by specialized craftspeople which hardly ever duplicated any specific device. Ford's innovative design reduced the sheer number of components needed as well as the wide range of competent fitters who had always created the bulk of the system procedure, offering Ford a huge advantage over his competitors.
Ford's first venture into vehicle assembly with all the Model A involved creating assembly stands which the whole vehicle ended up being built, generally by an individual assembler just who fit an entire element of the car together within one place. This individual performed equivalent activity over and over at his stationary system stand. To provide for lots more effectiveness, Ford had parts delivered as required to every work place. This way each assembly fitter took about 8.5 hours to accomplish their construction task. By the time ones Model T was being developed Ford had made a decision to use multiple assembly stands with assemblers moving from stand-to stand, each performing a specific function. This process reduced the installation time for every single fitter from 8.5 hours to only 2.5 minutes by making each worker entirely familiar with a certain task.
Ford quickly recognized that walking from stand-to remain squandered time and produced jam-ups inside manufacturing procedure as quicker workers overtook reduced people. In Detroit in 1913, he solved this issue by launching initial moving assembly-line, a conveyor that moved the automobile past a stationary assembler. By detatching the need for employees to move between stations, Ford slice the set up task for each employee from 2.5 moments to just under 2 moments; the moving construction conveyor could now rate the fixed employee. 1st conveyor range contained steel strips to which the vehicle's rims had been affixed. The steel pieces were mounted on a belt that rolled along the factory after which, beneath the floor, returned to first location. This lowering of the total amount of human being energy required to build a car caught the attention of vehicle assemblers around the world. Ford's size manufacturing drove the automobile business for almost five years and ended up being eventually used by almost every other commercial producer. Although technical developments have actually allowed numerous improvements to contemporary car construction operations, the basic concept of stationary employees setting up parts on a car as it passes their particular work channels has not yet altered significantly through the years.
Raw Materials
Even though the majority of a vehicle is virgin steel, petroleum-based items (plastics and vinyls) attended to express an ever more huge percentage of automotive elements. The light-weight products produced from petroleum have actually aided to lighten some designs by as much as thirty percent. Given that price of fossil fuels will continue to rise, the inclination for lighter, much more fuel effective automobiles will end up much more pronounced.
Design
Introducing a brand new type of car usually takes three to five years from creation to installation. Tips for new designs tend to be created to react to unmet pubic requirements and choices. Trying to anticipate just what people will want to drive-in 5 years is no small task, however vehicle businesses have successfully created cars that fit public preferences. With computer-aided design equipment, designers develop fundamental concept drawings that help them visualize the proposed automobile's appearance. Considering this simulation, they then construct clay designs that may be studied by styling professionals knowledgeable about exactly what the public will probably take. Aerodynamic designers also review the models, studying air-flow variables and performing feasibility scientific studies on crash tests. Only most likely designs have been evaluated and acknowledged are tool designers permitted to begin creating the various tools that'll produce the component components of the newest design.
Components
- 1 the car system plant represents just the final period in the process of production a car, for it is here now that the components furnished by above 4, 000 external companies, including company-owned parts companies, are brought together for installation, generally by vehicle or railroad. Those parts which will be found in the framework tend to be delivered to one location, while those who will include your body tend to be unloaded at another.